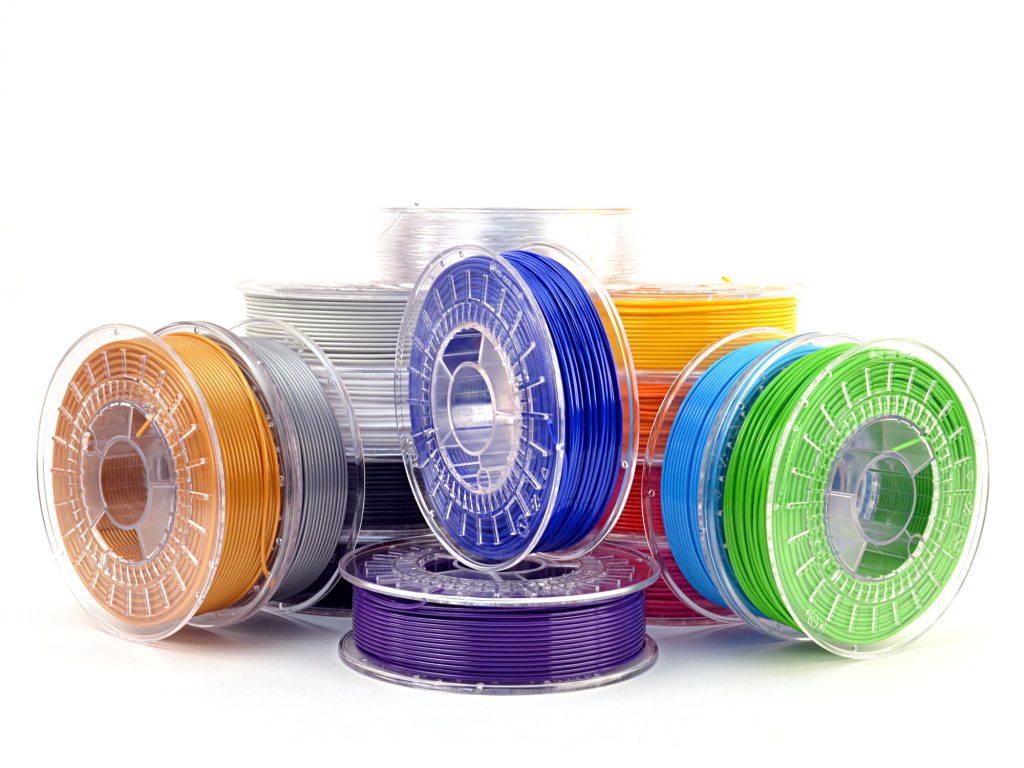
Materials
There is a wide range of materials (Filament / Resin) each with their own features, strengths and weaknesses. Sometimes it is hard to choose the most suitable material with your project in mind. This page is an overview of the most common materials that can be used on desktop 3D printers. For each material, we listed the features, pro’s and con’s so it can help you with choosing the right material.
For the full list of available materials please take a look at our online store
Material Info:
ABS
ABS (Acrylonitrile Butadiene Styrene) is an petroleum-based polymer. It is very resistant to high temperature which makes this material perfect for real-world components. It is a pretty cheap material allowing for cost effective prototyping. ABS is the go-to material for most 3D printers. Along with PLA, it is the most common material used for desktop 3D printing.
Features
ABS is available in a large array of colours which makes it popular among makers. Even the colorless ABS 3D printed object can be painted to any color. The material is mechanically strong, so you don’t have to worry about the lifespan of your model.
If you’re using ABS it is advised to print at 220° and 250°centigrade. To avoid bending and warping you will want to print with ABS on a heated bed (from 50° to 100°C) to ensure gradual cooling of the material. ABS gets a shiny, glossy look when processed with acetone vapour as this solution has the property to melt the upper layer of the printed object, making it smooth and shiny.
The biggest downfall of ABS is that it is a nonbiodegradable toxic material that releases toxic fumes at high temperatures and smells awful.
Pros
Cheap
Highly Available with a large variety of colours
Applicable to just about any printerWarping
Mechanically strong
Longer lifespan
Cons
Toxic
Requires heated bed
Warping
Not suitable for use with food
PLA
Made from renewable resources, Polylactic Acid is green 3d printing material. It has a moderate price point on the market and has various desirable properties and technical specifications which makes it the perfect 3D printer filamentfor hobbyists.
Features
PLA’s general print temperature is between 180° and 220°. It is a slightly flexible material, but it generates a smoother outer shell of the printed object. Due to the fact that it is made of corn starch, PLA is not toxic and releases a pleasant sweet smell. PLA is preferred for 3D printing smaller objects.
This material is generally considered easier to print than most other materials, however, the postprint processing of PLA objects is much more difficult than those printed in ABS. PLA is available in a wide variety of blends such as wood, bamboo (mixing the standard plastic with fibers), copper, bronze (powder mix), and glowing effect (phosphorescent pigment).
Pros
Easy to print
Easily available in a variety of colours
Can be printed on a cold surface
High speed printing
Low warping
Cons
Not very sturdy
Can deform when exposed to heat
Difficult to post-process
Nylon
Nylon is a strong and durable synthetic polymer with a translucent silky finish, also called white plastic. It is also sold for a moderate price which makes it widely used for the production of household items. Want to get started with printing Nylon? Check out our in-depth article here.
Features
Nylon is a flexible material, with a natural white color, but it can be painted in any color with an acidbased dye. With nylon you can print moving parts, making it ideal for hobbyists. Although nylon prints have a somewhat rough surface, it can be smoothed out. It is recommended, however to avoid nylon for printing small elements as the smoothing procedure can damage them. Taulman 618, Taulman 645, and Bridge Nylon are the most popular types of material for 3D printing. Taulman 3D printing materials are known to have high interlayer bonding, ensuring great durability and resistance of the printed model.
Just like PLA and ABS, Nylon material absorbs moisture from the air. This fact affects the quality of the print. Also, the moisture that gets absorbed by the material is the one to blame for the fumes released during printing. To avoid this, it is advised to store Nylon in airtight containers.
Pros
High durability
Flexible yet strong
Easily dyed by leaving it soaked
Produces smooth prints
UV and chemical resistance
Cons
Constantly meant to be kept dry in moisture free containers
Printer suitability varies
May require alterations to printers just to use
Can expire
Nylon sometimes shrinks during prints, and thus results can be imprecise
Polypropylene (PP)
PP or polypropylene is a plastic used for many different purposes such as textiles, ropes and stationery. It is also resistant to multiple chemicals and solvents. PP is one of the most cost-efficient materials. The most common shaping technique for producing PP is injection molding. It ranks as one of the most coveted materials in the world.
Applicable Technologies – FDM/FFF
Features
Polypropylene can be strengthened by copolymerising it with ethylene. It can be used as an engineering material. It is also resistant to fats and almost all organic solvents at room temperature. PP can be dissolved in nonpolarity solvents such as xylene, tetralin and decalin.
It is very stiff and strong, and is thus used heavily for ropes and small components. Another great aspect of polypropylene is that since it is so widely used, it can be easily recycled for new filament. While it can be comparatively expensive, it’s recyclability makes it a bit more cost-effective.
However, PP does have it’s downsides. While it retains colour during heating, it has low solubility when it comes to dyes. Because of its excellent electrical insulating properties, polypropylene has a tendency to retain static charges caused by processing and handling. This condition also attracts dirt to the polymer surface.
Pros
Recyclable
Resistant to many solvents
Does not require complex heating apparatus
Stiff and strong
Colour retention
Resistant to bacterial growth
Cons
Impacted by UV
Expensive (more so than PE)
Heavy warping
Difficult to print (very few printers currently manage it)
ASA
ASA is a production grade thermoplastic that is most commonly associated with FDM/FFF printing. It can be considered an alternative to ABS. Acrylonitrile Styrene Acrylate was created chemical company BASF in the 1970’s. It has massive strength and resilience.
It is weather resistant, and therefore used in many outdoor appliances. Printing it can require precise temperatures and minimal cooling on the fan. It also needs a controlled printing area, so ensure that you have some form of closed chamber to prevent alteration caused by air flow.
Applicable Technologies -FDM/FFF
Features
Since it is strong, heavily resistant to environmental factors and UV, ASA is considered useful for creating objects for the outdoors. It is also used to manufacture plastic components one would find in cars. ASA generally melts at the same temperature as ABS but is much rougher on the printer’s hardware. For this reason, it isn’t quite as common.
It has less shrinkage and can be molded into complex shapes. It is less prone to turning yellow while left in the sun. On the downside, ASA can crack if it is cooled too quickly. This means turning your cooling systems to a lower temperature.
Pros
More durable than ABS
Heat resistant
UV resistant
Less wear and tear over time
Minimised shrinkage
Cons
More expensive than standard thermoplastics
Less availability of filaments
Only certain printers can process it
Requires more precision with cooling
Polycarbonate (PC)
Polycarbonate is a thermoplastic that is also known distributed under the trade name Lexan. It is generally lightweight and transparent. It is often used in industries as diverse as CD production, riot gear and sun glasses. Needless to say it has a diverse range of applications.
Polycarbonates are easily thermoformed and molded. This has been one of the reasons it is a staple of so many products as an engineering plastic.
Applicable Technologies- FDM/FFF
Features
Due to its high heat deflection (heat resistant up to 116 °C) PC is incredibly useful for high temperature applications such as the inside the hood of a car. It also has a great flexibility and snaps right back into its original shape when bent or twisted. It can be as transparent as glass while possessing half its density. Yet, it has a density and tensile strength higher than both PLA and ABS. PC is ideal for anyone looking to produce a strong yet flexible transparent print.
It is also soluble in dichloromethane, it melts at temperatures of 260 – 300 °C and it will also require a heated bed (about 90 °C) to produce the best results. In general the closer to 300 °C, the better the print quality you can get (although, its transition temperature is quite good, so reaching 300 °C is not an absolute necessity).
Pros
Flexible and durable
High tensile strength
Not extremely difficult to print
Transparent
Diverse applications
Standard melting temperature
Cons
Necessitates use of heated bed to avoid warping
Varying levels of filament quality that depend on price
Environment needs to be kept warm for optimum quality
PET/PETG
PET and it’s derivative material PETG are one of the most popular materials in the world. Even if you don’t know them by name, you’ve definitely seen them used in plastic bottles, in clothing fiber and in everyday consumer products. PETG is a modified version of PET with notable differences.
Applicable Technologies – FDM/ FFF
Features
PET and PETG are easy to print with, however, they require a very precise temperature environment. This often leads to a lot of experimentation to get the exact parameters right. PETG and PET don’t necessitate a heated bed but it does help. The materials are not soluble in acetone.
The core differences between PET and PETG are durability (PETG has more), reaction to overheating (PET becomes brittle), Impact resistance and the presence of glycol in PETG. Recyclability is a massive advantage of PET and PETG. This can allow for the reuse of failed prints. They are generally transparent.
Pros
Low warping
Recyclable
Easy to print and has good layer adhesion
Durable
Can be sterilised
Good for food and drink containment
Cons
Requires very accurate temperature conditions to get right
PET becomes brittle from overheating (though not PETG)
PETG can be weakened with UV light
Prone to scratches (more than PLA)
HIPS
HIPS stands for high impact polystyrene. Polystyrene is one of the most common materials in our daily lives. HIPS is a low cost material, with a higher strength level than the standard polystyrene. HIPS is used for various things like plastic signs and thicker containers.
Applicable Technologies – FDM/ FFF
Features
HIPS can be used as a support material since it can be erased using limonene. HIPS is comparable to ABS in terms of ease of use. The core difference is its ability to dissolve. HIPS undergoes a high level of warping. However, with a well-balanced temperature level, it can produce very smooth layers.
HIPS is very malleable and can be used to make intricate structures. It is best used with a heated bed because it needs a constant temperature. In fact, without a constant flow of heat can cause HIPS to clog up the nozzle and delivery tubes. This means that it can make it difficult to print with 2 nozzle systems. It also has another downside, which is that it produces very strong fumes, so it’s best used in a ventilated area.
Pros
Very smooth
Very durable
Wide range of applications
Dissolvable and great as a support material
Cons
Strong fumes
Constant heat flow
High level of warping/ can cause clogging in the extruder
TPU/FLEX
Thermoplastic Polyurethane is among the more flexible thermoplastic options out there. It is used for multiple different everyday products like phone cases and bendable parts. TPU is actually a blend of various different polymers. It is sometimes referred to as a thermoplastic “rubber” due to its texture and flexibility but both of those are largely dependent upon the type blend of materials in the filament.
Applicable Technologies – FFF/ FDM
Features
It’s primary advantage is that it can be flexible. Various blends can give it additional characteristics, mostly altering its strength and malleability. It doesn’t necessitate a heated bed but the extruder needs to be very good at maintaining a consistent temperature.
As a flexible material it is far harder to print for certain printers. Bowden extruders may find it difficult to print because it can tangle up due to its elastic-like properties. Thus, direct drive extruders are more desirable as they are far closer to the printhead.
TPU has a decent level of chemical resistance. It can resist oils, greases and a fair variety of chemical solvents. The material is fairly tough against abrasions and bruises. This makes it better for use in functional parts considering.
Pros
Uniquely flexible
Range of blends and characteristics
Resistant to oils, greases and multiple solvents
Low abrasion
Low shrinkage
Cons
Consistent temperature from the extruder required
Requires direct drive extruder (Bowden extruders may tangle it)
PVA
Polyvinyl Alcohol is a water soluble material that is great for printing but can also act as a support material. This makes it very useful for complex designs where support removal can be damaging or tricky. Thus many users print support with it can leave the result in a body of water overnight and retrieve their desired print.
Applicable Technologies – FDM/FFF
Features
It’s primary feature, as mentioned earlier, is its water solubility. Unfortunately, this makes it unsuitable for outdoor goods. This material is a great support material alongside PLA because it is soluble in water and PLA is completely unaffected by water. Additionally, it has a melting temperature that matches with PLA.
Aside from its water solubility, PVA also absorbs moisture. This means storage can be slightly cumbersome. It does not require a heated bed. It bonds very well against most thermoplastics, as support materials should.
Pros
Great for complex prints
Water soluble
Bonds very well to other thermoplastics
Biodegradable
Safe to print
Cons
Needs to be contained in a moisture free environment
Impractical for functional prints
Acrylic/Resin
Acrylic covers a wide array of plastic materials with multiple functions. However, there is a certain class of acrylic that can be printed with DLP or SLA technology. Acrylic based UV reactive resins are not as common as other thermoplastics.
Acrylic is also known as plexiglass. The material can be used for a lot of applications and is widely available. It often serves as a lighter alternative to glass. It is shatter resistant and embodies range of durability (from flexible to hard) depending on the version of plexiglass being used.
Applicable Technologies – DLP / SLA / LED
Features
Acylic covers a broad range of wavelengths. It is suitable for laser, DLP and LED systems. Ultra short exposure time which means quicker printing. It has a very low level of shrinkage. Its qualities and attribute vary wildly. You have hard, soft and castable types. This material is known for a high chemical resistance
Resins also comes in a range of colours. It is generally non-toxic, making it ideal for desktop printing. Since it is such a versatile substance, it has a divers range of applications.
Pros
Many applications
Suitable for multiple UV or LED based systems
Low shrinkage
Allows a wide spectrum of strength and flexibility
High chemical resistance
Non-toxic
Cons
Rarer than most materials
Expensive
Heat can cause premature polymerisation
Needs to be stored safely due to high photo-reactivity
Can expire