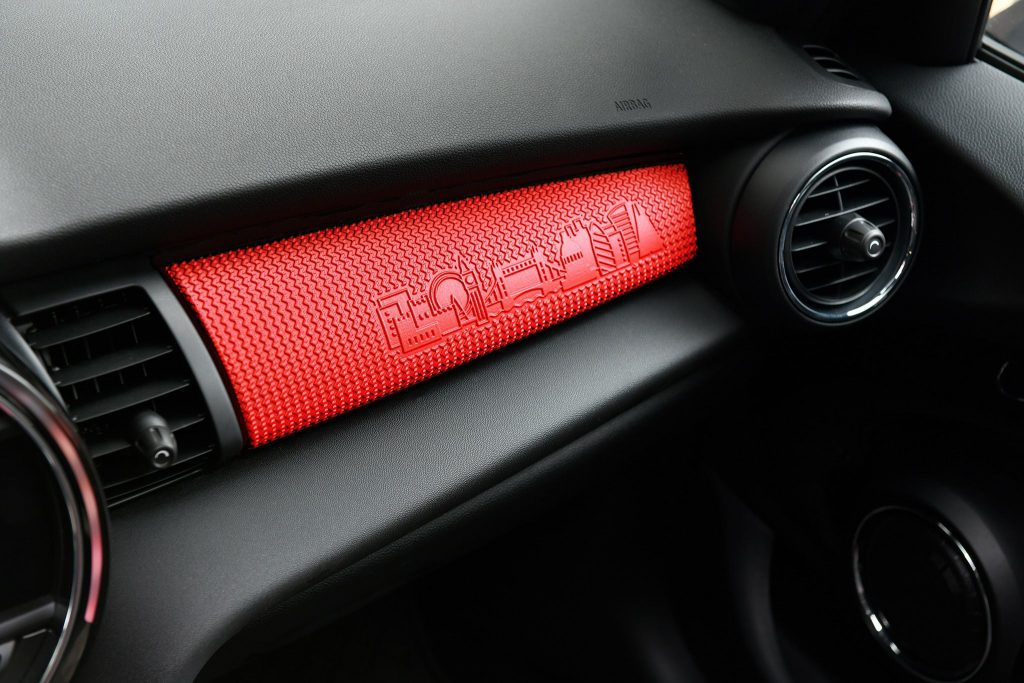
Automotive
Create Assembly Aids & End Use Parts
By building durable concept models, prototypes, tooling and low-volume end-use parts in-house, automotive engineers and designers can work more iteratively, test more thoroughly and move confidently into production.
Why 3D Printing for Automotive Design?
-
Replace Expensive CNC Production
By replacing expensive and lead-time critical CNC-milled parts with in-house manufactured plastic parts, you can dramatically reduce your production costs. The printed plastic parts also perform better technically, weigh less, and are well suited for the production of complex bodies that, when using conventional metal-cutting processes, would be very difficult and costly to produce.
-
Print Parts on Demand
Instead having to keep inventory for slow moving parts or back to back order from overseas supplier, you can now just print out the parts whenever needed. Cost and time saving is another benefits.
-
Create Better Assembly Tools
For hand-held devices used on the assembly line, engineers can employ 3D printing to make ergonomically designed assembly aids that perform better than conventionally made tools.
-
Test and Identify Design Problems
In some cases using CAD models alone is not as effective at finding design problems as a 3D printed physical part – you can easily identify a component issue that may have been missed in the initial design stage.
1 thought on “Automotive”
Comments are closed.
3reprimand